Geotechnical Engineering
Geotechnical engineering applications were Ryobi G’s flagship services back in 2000. After years of continuous improvement, Ryobi G is now a leader in geotechnical engineering works in Singapore, securing key projects in public and private sectors.
Our geotechnical engineering techniques
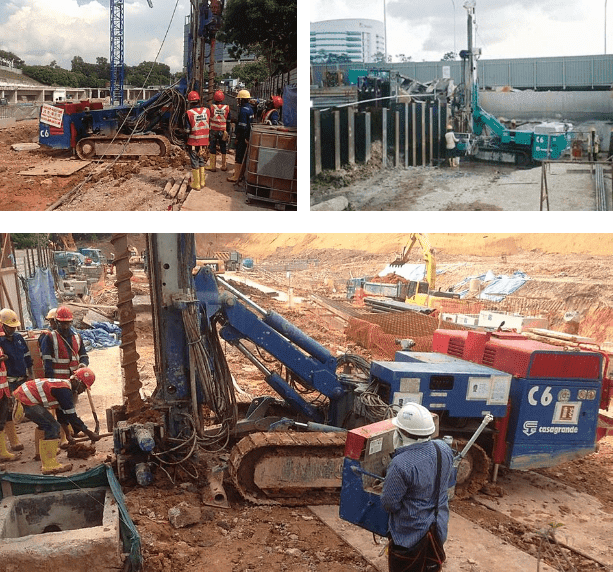
Using soldiers piles and tension piles as part of our micropile capability. There are many types of micropiles to date.The most commonly known ones are; soldier piles, driven piles, soil nails and ground anchors.
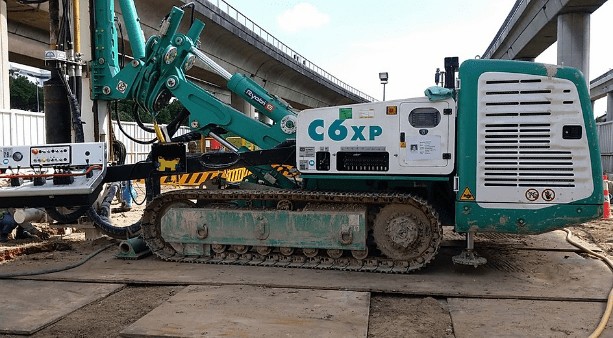
Micropile works with C6XP along Upper East Coast Road.
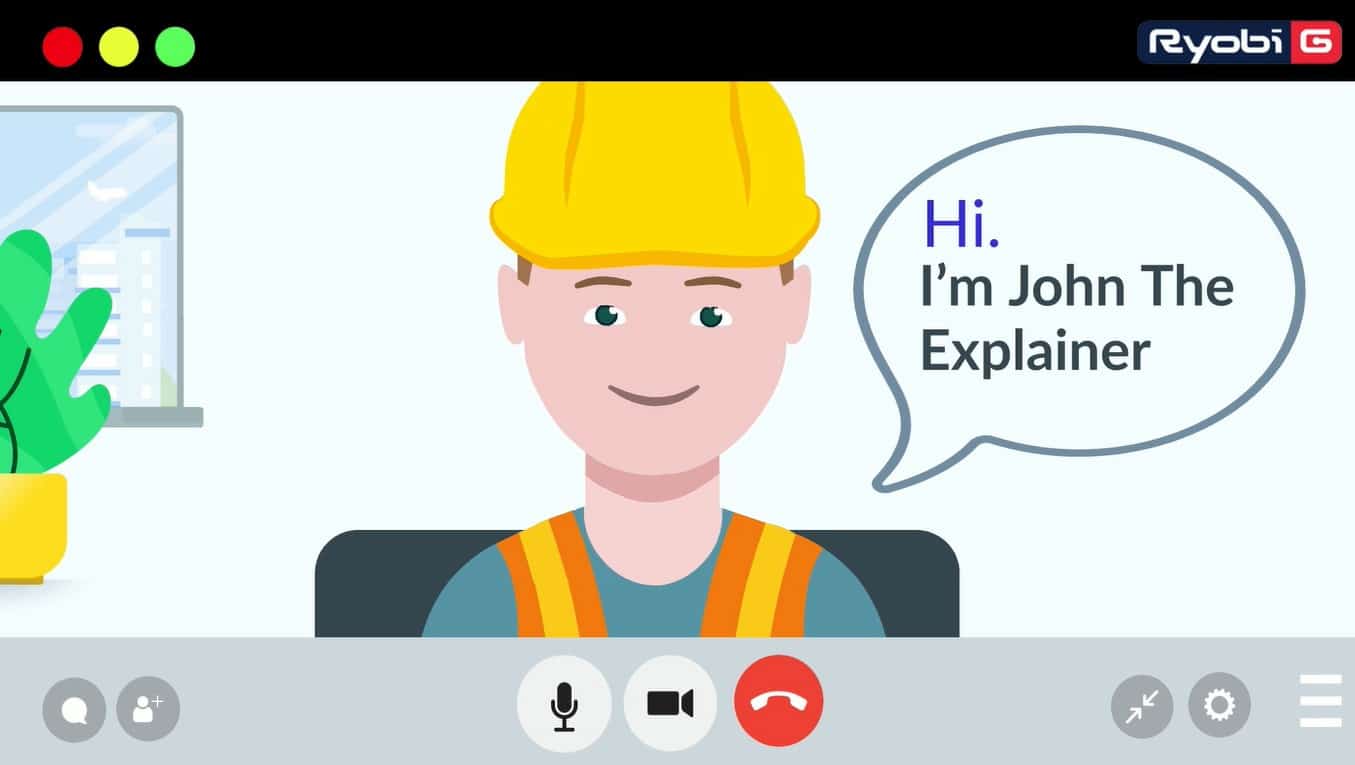
Preliminary pile load test of micropiles.
MICROPILES
Micropiles are considered as one of the deep foundation techniques to transfer load from structure to the competent bearing stratum at deep depth, especially for sites with restrictions attributed to limited workspace and low head room.
Micropiles consist of two (2) typical types according to its installation method, i.e. driven type (e.g. steel beam, pipe or rail, etc.) and bored type (e.g. cast in-situ using rebars and cement grout similar to bored piles except in smaller diameter ranging from 75mm to 300m).
Ryobi G specializes in the construction of bored type of micropiles using C5, C6, C6XP machines.These machines allow continuous drilling with bentonite, water or even cement grout. Ryobi G has the appropriate machines for different situations faced in the piling works. For instance, we counter space constraints with the availability of small-sized machinery that are versatile and able to maneuver in tightly enclosed areas.
History of micropiles works dated back to post World War II for damaged buildings. Today, it is used widely to stabilize old structures especially heritage buildings and increase load capacity of buildings under restricted and sensitive environment. In fact, it is much more economical for contractors to strengthen the foundation than to tear down existing building and construct a new one.
The advantages of micropiles are aplenty. Micropiles are generally smaller, lighter, less impact to the surrounding properties and more economic for special cases as compared to other deep foundation technique. From an environmental standpoint, installation of micropiles through the rigs is low emission with limited vibration and noise disturbance. The general properties of micropile; with good capacity in resisting compressive and lateral loads have also made this technique very popular in deep foundation construction and excavation works.
Micropiling also has a huge range of applications and they are not only limited to the below:
a) Underpinning works
b) Structural and foundation support
c) Supporting new load and retrofitting
d) Pile wall
UNDERPINNING
Underpinning strengthens the foundation of an existing structure via additional structural elements (e.g. micropiles) or foundation soil improvement (e.g. grouting). Underpinning can be used when there are structural changes, weakened foundations, and to alter the current foundation.
Grouting is also a good alternative to a conventional piling method used in underpinning work. Compared to inserting high strength steel beams, grouting is more cost effective. For an underpinning work done in a shopping mall, we saved our client over one million dollars by strengthening the existing structure rather than building new ones.
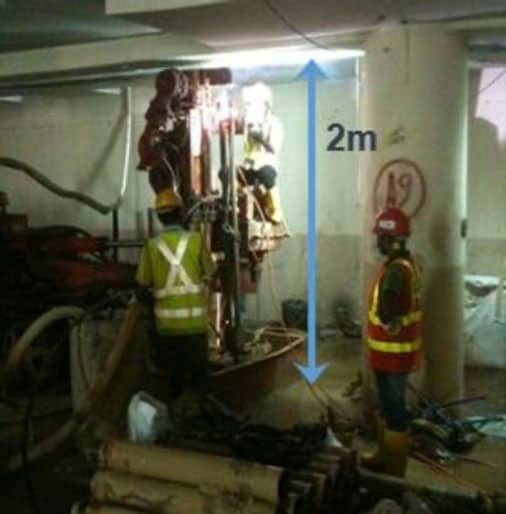
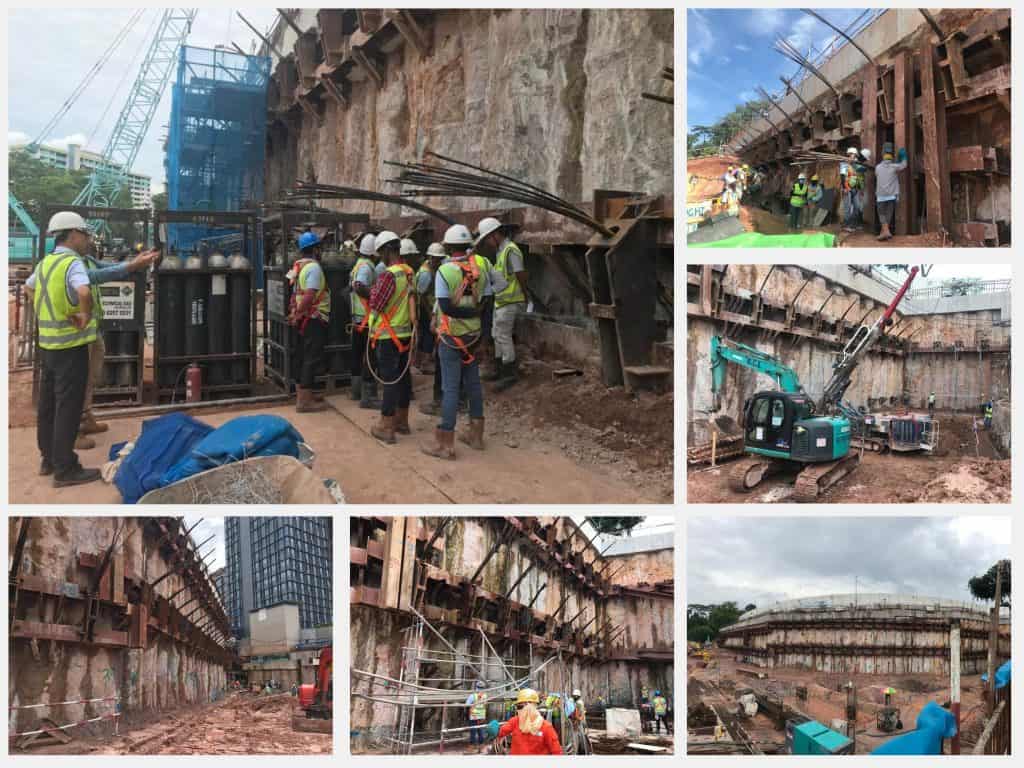
EARTH RETAINING SYSTEM
Earth retaining system (ERS) is a mean of providing structural support to construction site in the early phase of construction, e.g. excavation stage. There are a multitude of methods for supporting the ERS; soil nailing and ground anchor are known as the most commonly used ones. Despite their primary function that is to provide structural support, they are also suited for different situations.
SOIL NAILING
In Geotechnical Engineering, no single technique is restricted to only one aspect of ground improvement. Taking soil nailing as a prime example, it reinforces soils slopes and excavation to enhance bearing capacity and stability. There are several other techniques that offer different uses and applications, depending on the nature of the situation.
Soil nailing is typically suited for resisting shallow slip failure in incompetent ground whereas ground anchor is meant for resisting deep slip failure . They have different mechanism to provide structural support too. Soil nailing generates tensile force in deformed slope whereas ground anchor employs heavy stress to minimize deformation.
The main advantages that soil nailing bring about to slope stabilisation techniques is that this method is relatively inexpensive and the installation process is fast and straightforward. In the event of soil nail installation, the machines are usually small in size, which means the process of soil nail installation does not require huge amount of space to work about. Soil nails could be used on heterogenous ground which means the ground could be a mixed of gravels and hard rock. In addition, the most important technical aspect of soil nails is that it limits the deformation in area of interest and when these soil nails are stressed, the load will be redistributed to the other soil nails. A combination of soil nailing works and guniting (shotcreting) or grid-beam system is commonly used as the slope stabilization system in this region.
General applications of soil nailing include but not limited to the below:
a) Slope repairs in urban and suburban area
b) Reconstruction of retaining structures
c) Provision of long term stability to existing structure without destructive test
d) Retrofitting bridge abutment
e) Stabilisation of natural/artificial steep slope.
f) Soil nailing
An alternative use of GFRP soil nailing has been popular in the recent years. We are proud of our capability to carry out soil nailing via the use of steel rebar and GFRP (Glass Fiber Reinforced Polymer).
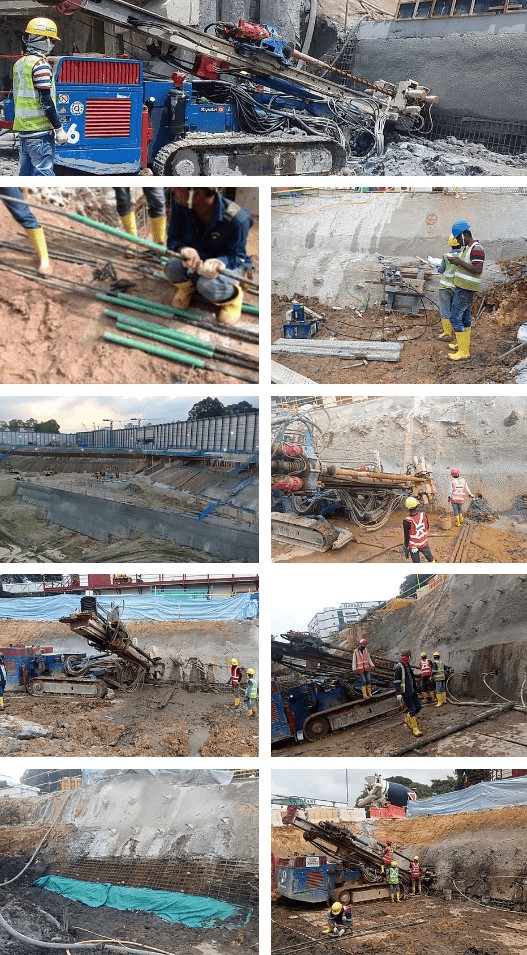
Soil nails made of steel bars or GFRP are usually installed with C6 machines. Guniting is conventionally carried out after the installation of BRC and soil nails.
To date we have used the 2 different types of soil nails and with the thickness of gunite ranging from 150mm to 220mm.
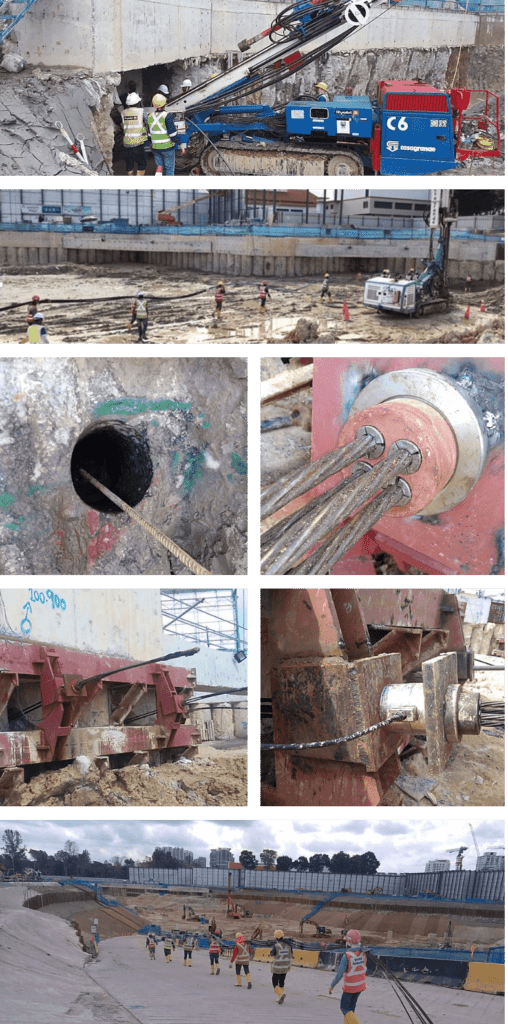
Ground anchors are usually installed using with C6/C6XP machines to form a reaction/resisting system with the steel brackets and the steel waler beams.
GROUND ANCHORS
Ground anchor employs heavy stress to minimize ground deformation and is competent in resisting deep slip failure where competent stratum for generating the anchor bond resistance is located at depth.
Besides the conventional multi-strands tendon used in the ground anchoring works, light and versatile, Glass Fiber Reinforced Polymer (GFRP) ground anchors are easier to handle as it does not create underground obstruction in long term compared to conventional ground anchors. Ryobi-G also boast of being the first contractor in this region to employ the use of GFRP ground anchors in the construction of Singapore MRT-DTL3..
Both the conventional and GFRP anchors come in a wide range of length and capacity which are suited for different use, e.g. temporary supports to a structure or a retaining system.
Conventional anchors (steel) are more economical than GFRP anchors, however there are issues from underground obstruction (if not removal type) and corrosion effect in long-term application which requires protection measure, e.g. corrosive protection system. GFRP ground anchors are not affected by climatic changes are can dual its role as a permanent or temporary support structures. GFRP ground anchors usually more versatile and preferred (as required by site requirements).
The advantages of ground anchors are aplenty. This technique is economical and able to withstand high load despite heterogeneous ground conditions, which also create minimal impact on the site/construction. Similar to soil nails, this ground stabilization method does not require huge amount of working space and ground anchors could be installed easily by the mobility of the machines.
General applications of ground anchor include but not limited to the below:
a) Slope stabilization / protection
b) Excavation in close proximity to existing properties, e.g. buildings and infrastructures, etc.
c) Supports to bridge abutment
d) Uplift resistance
e) Supports to retaining system, e.g. sheet pile wall, bored pile wall, diaphragm wall and RC retaining wall, etc..
GUNITING / SHOTCRETING
Slopes that have been stabilized through the use of soil nails, ground anchors or other ERSS are usually placed with BRC wire mesh followed by a final layer of gunite to enhance surface protection. In the construction phase, guniting is also used for stabilisation to temporary cut, earth retaining system and even used as the lining in tunnel construction and strengthening/protection measures for rehabilitation work.
Guniting, also commonly known as shotcreting is a process where a fresh mix of cement is sprayed onto them the treatment area to form a strong cement layer (with or without BRC wire mesh or rebars) after hardening. The gunite takes form of the structure despite the irregularities on the surface, thus increases the surface retention and provides surface protection against erosion and shallow slip failure. The end product of guniting is to let the treated surfaces obtain high strength and low permeability.
The versatility of guniting has brought about many advantages in the construction phase. The preparation of cement mix and process of guniting are relatively fast and these save time in the construction work. In the guniting process, the handler sprays the guniting mix through a nozzle on the treated surfaces repeatedly a cement layer of at least 150mm to 200mm thick is formed. As compared to concrete, guniting is relatively faster, more economical and less labour intensive.
One of the major advantages of guniting over concrete is that guniting can takes the shape of curved and folded sections, regardless of the profile of the treated area in both the horizontal and vertical directions.
Besides being able to take the shape of the treated area, the wetness and dryness of the guniting could also be adjusted to suit the workability and other requirements.
Applications of guniting:
a) Slope stabilisation
b) Tunnelling
c) Retaining walls
d) General structural reinforcement
e) Restoration works.
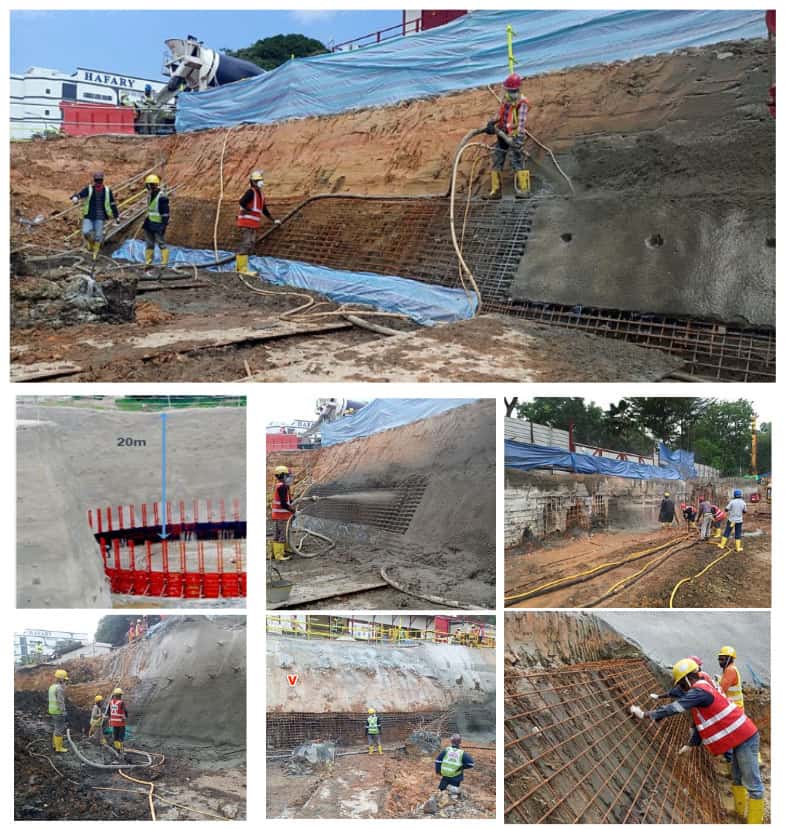
Ryobi G has successfully completed guniting at 20m height.
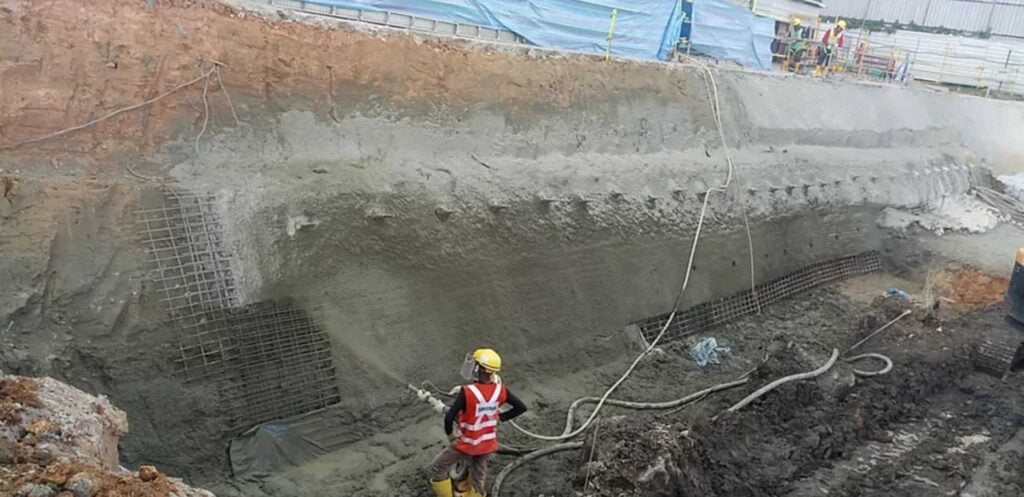
Our workers spraying gunite for repair works.
GEOCELLS / EROSION CONTROL
Cellular Confinement Systems (CCS) which also known as geocells are used mainly for soil stabilization and erosion control. Similar to guniting, geocells are used for structural reinforcement for retention and support against surface slip. It usually employs the use of honeycomb-shaped high density polyethylene (HDPE) on slopes which are steep and with irregular topography. Not only does geocells provide functional use of ERSS, it is able to give an aesthetical boost to the environment when these cells are vegetated. The maturation of vegetation will further enhance the stability of the slope through interlocking of plant roots.
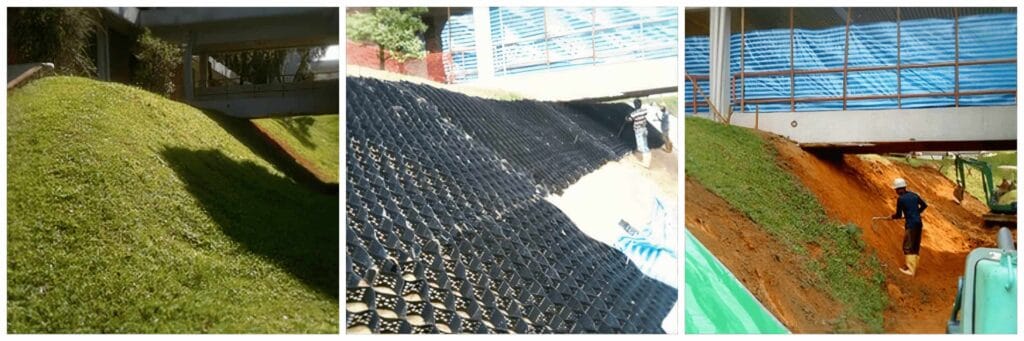
Geocells: One of our local project employing the use of geocells which can help in erosion controls.
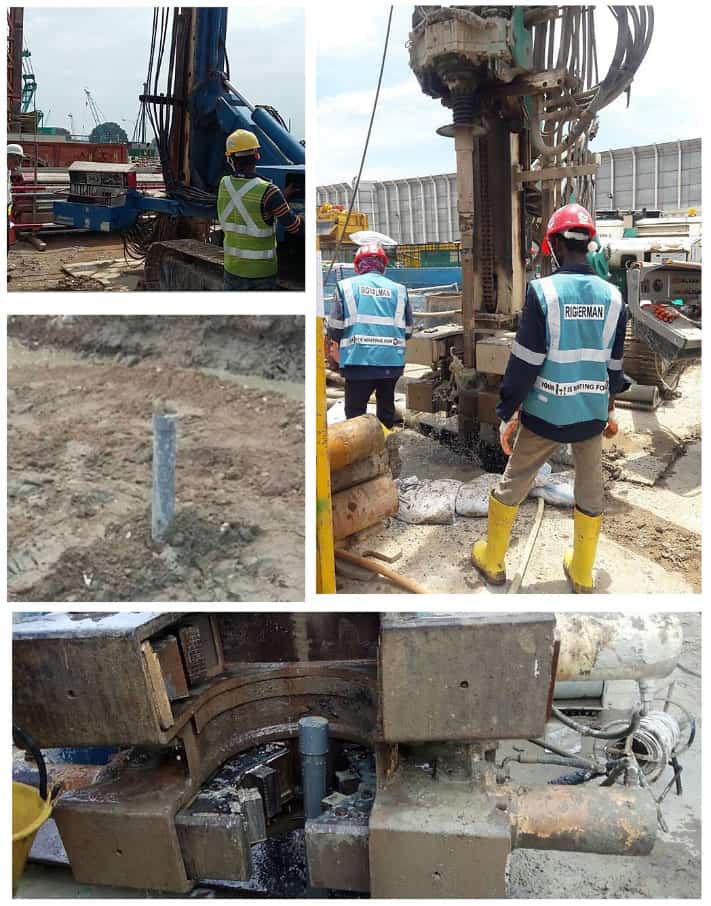
Relief well used in DTL3 -Extension
RECHARGE AND RELIEF WELL
Relief Well:
This technique has been used over the last century with the primary use of tapping underground fossil fuels. Over the years, relief well have been employed in the field of oil and gas industry as well as geotechnical engineering industry. Groundwater control is an important measure to control erosion and keep groundwater from entering excavation. Relief well are used to reduce excessive porewater pressures in stratified ground condition. This temporary control is typically drilled before excavation goes beyond the piezometric level in the aquifer. When excavation continues, water will overflow from the well by disposed passively or through pumping.
The advantages of relief wells are that they generally easy to install and cost effective.
The nature of relief well can also be temporary or permanent depending on the needs of the nature of excavation work.
Relief well also have a huge range of applications as shown below:
a) Geotechnical engineering
• To relieve groundwater pressure for stabilizing excavation against push-up failure in soft clay and piping/boiling failure in sand
• To stabilize foundation system against uplift effect
b) Pit mining
c) Oil and gas industry
Recharge Well:
When water seeps into an aquifer, it is known as ‘’recharge’’ and hence the name recharge well suggests that water that seeps through a pipe into an aquifer in an excavation site is known as recharge well.
Usually, recharge wells are used in deep excavation for minimizing drawdown effect via returning water back to the aquifer away from the site dewatering system. It is typically use for controlling consolidation of compressible soils due to the change in porewater pressure causing adverse effect (e.g. differential settlement or damage) to structures on top of the compressible soil layer.
The 2 most commonly known techniques of recharge well are known as:
a) “Injection” where water is directly pumped into the ground via the stalled wells to recharge the loss in the aquifer under injection pressure.
b) “Gravitational force’ where water flow from the elevated water tanks and seep into the aquifer under gravity effect.
The selection of either techniques for recharge well largely depends on the site condition and projection requirements.
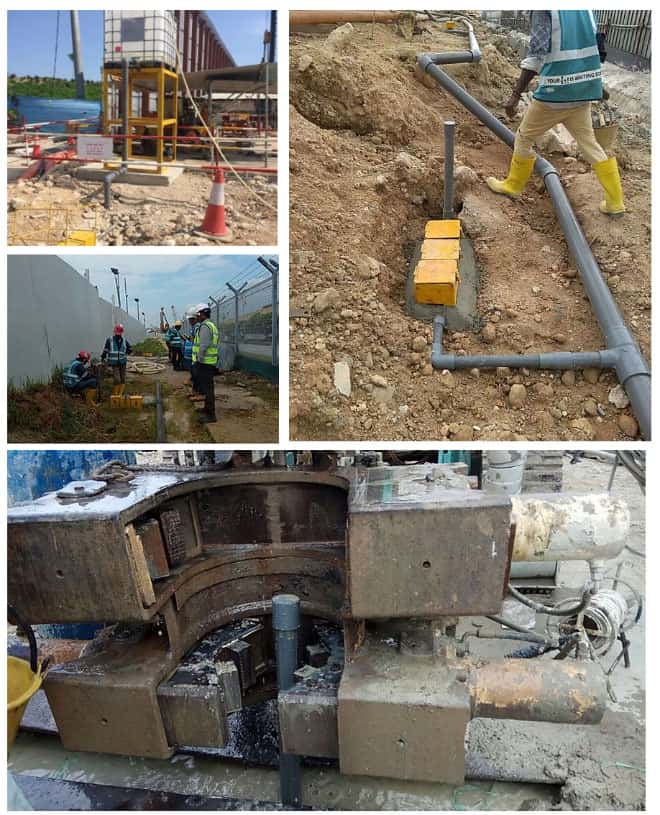
Recharge well used in DTL3 -Extension
GEOTECHNICAL DESIGN AND ANALYSIS
Ryobi G offers comprehensive design and build services for all our geotechnical services offered. We have vast pool of qualified engineers who are IT-savvy, using programs which allow 3D visualization of any structural conflicts. After meticulous planning with our prospective clients, this allows smooth transition from the designing phase to the construction building phase which can collectively save our clients’ time and effort.
Our Machines:
– Casagrande
Used for projects involving soil nailing, micropiling, ground anchor, underpinning, recharge and relief wells
– Casagrande C6XP
An improvised version of C6 which can be used for soil nailing, micropiling, ground anchor, underpinning, recharge and relief wells.
– Bunker-Teksped
Used for projects involving guniting/shotcreting
– Hanjin
Used for projects involving micropiling, recharge and relief wells
– Soilmec
Used for projects involving micropiling