3D Laser Scanning
3D laser scanning is a powerful surveying technique that we at Ryobi-G use to help professionals like Engineers, Designers, Architects, Asset Managers etc. develop digital 3D models specific to their needs.
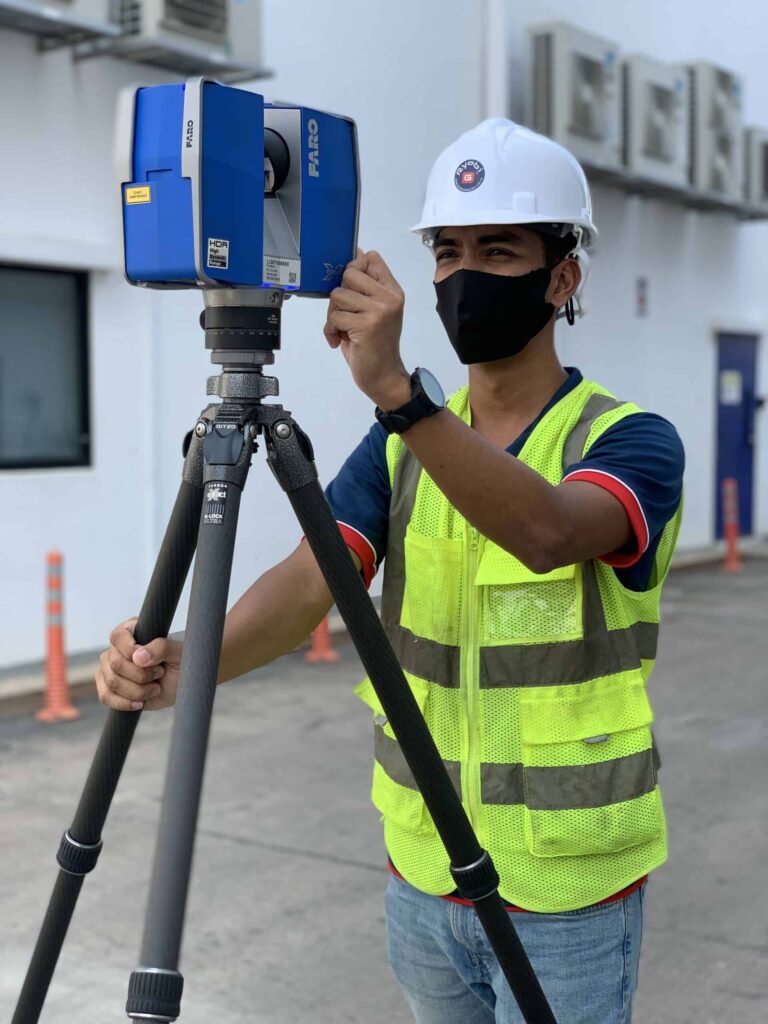
3D Laser Scanning (3DLS) is a remote mapping and imaging technique that uses lasers to capture an object’s digital representation in 3-dimensional space as efficiently and as accurately as possible.
We at Ryobi-G use world-class 3D laser scanning equipment from renowned brands such as Leica© and Farro© to assure the data we collect meets the highest of industry standards. This enables us to create digital (3D) representations of large, complex structures such as building interiors, processing plants, as well as dynamic environments like constructions sites.
Applications for data collected from 3D laser scans are used regularly by professionals to help with decision making throughout a project’s life cycle(s) across various sectors and industries. From cloud point registration, to rendered digital 2D scale drawings and / or 3D models – and everything in between, we have the resources to deliver results.
Some applications of our 3D laser scanning
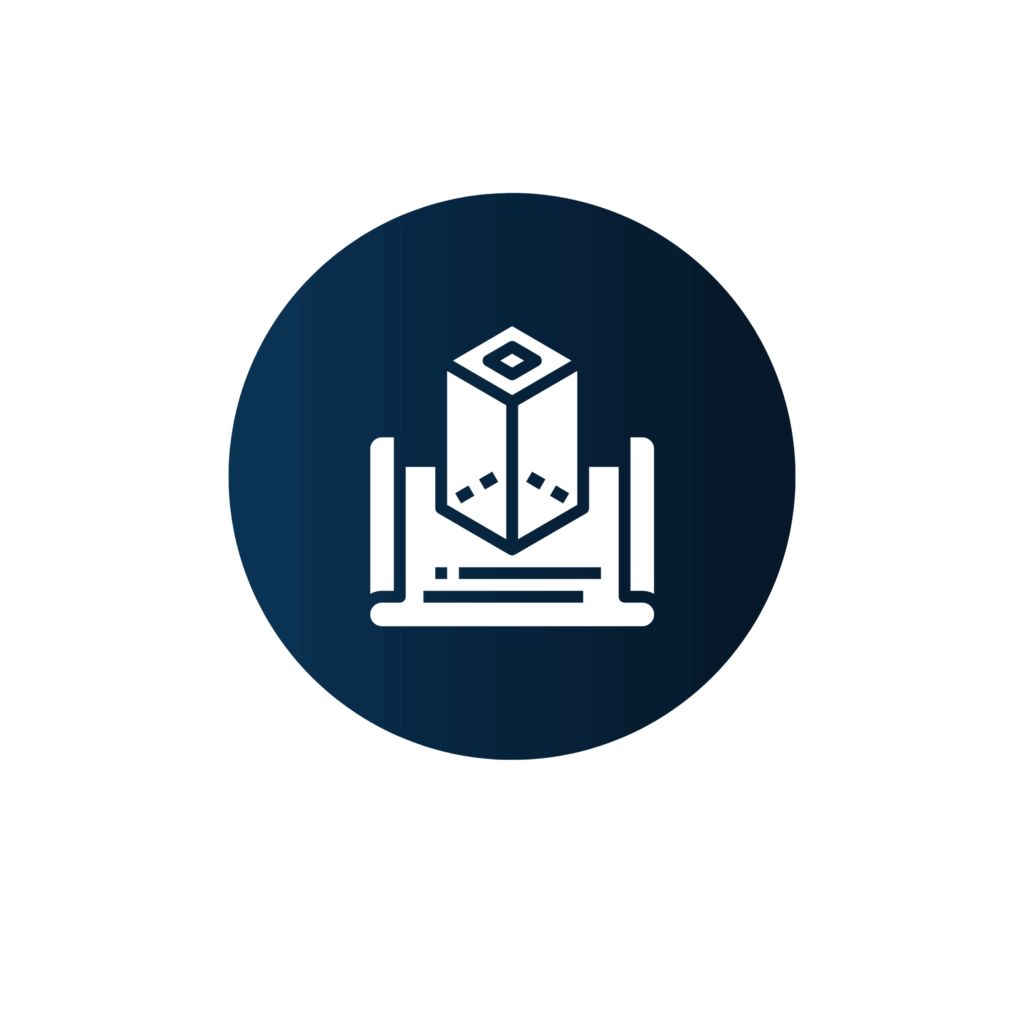
Documentation
Capture the pre and post-work surface conditions of buildings and other types of civil structures in 3D digital representations for archives and baseline records.
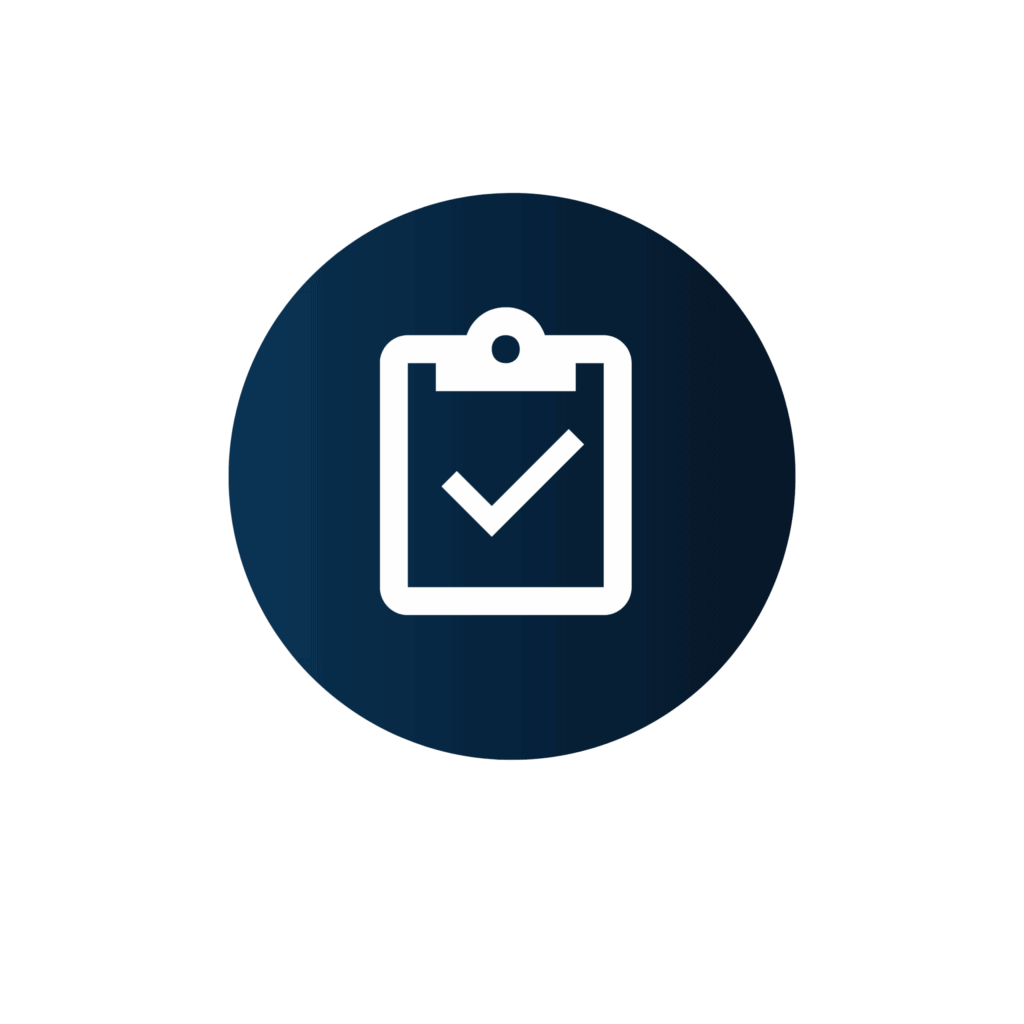
Monitoring
Road surface settlement monitoring for prioritisation of repair works
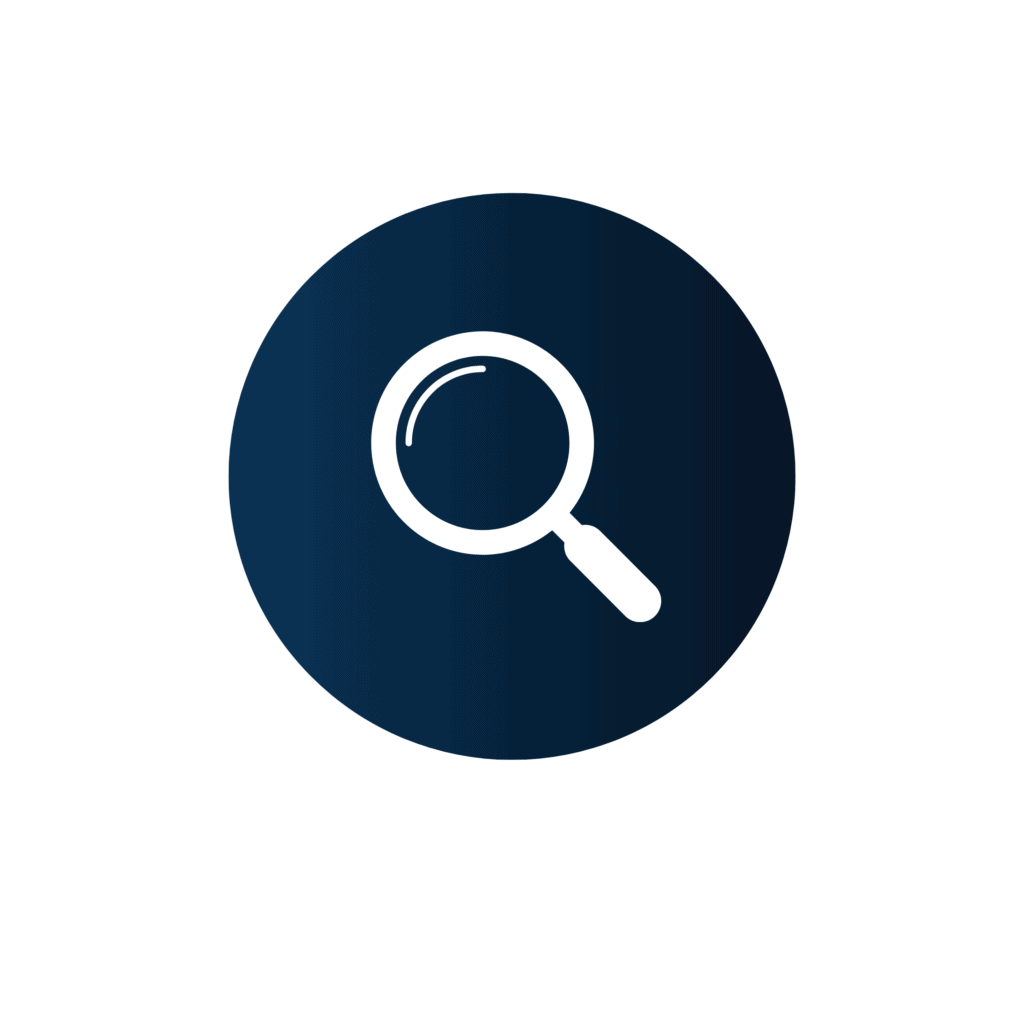
Clash Detection
Periodic scans to detect positional or alignment deviations of objects and features over time.
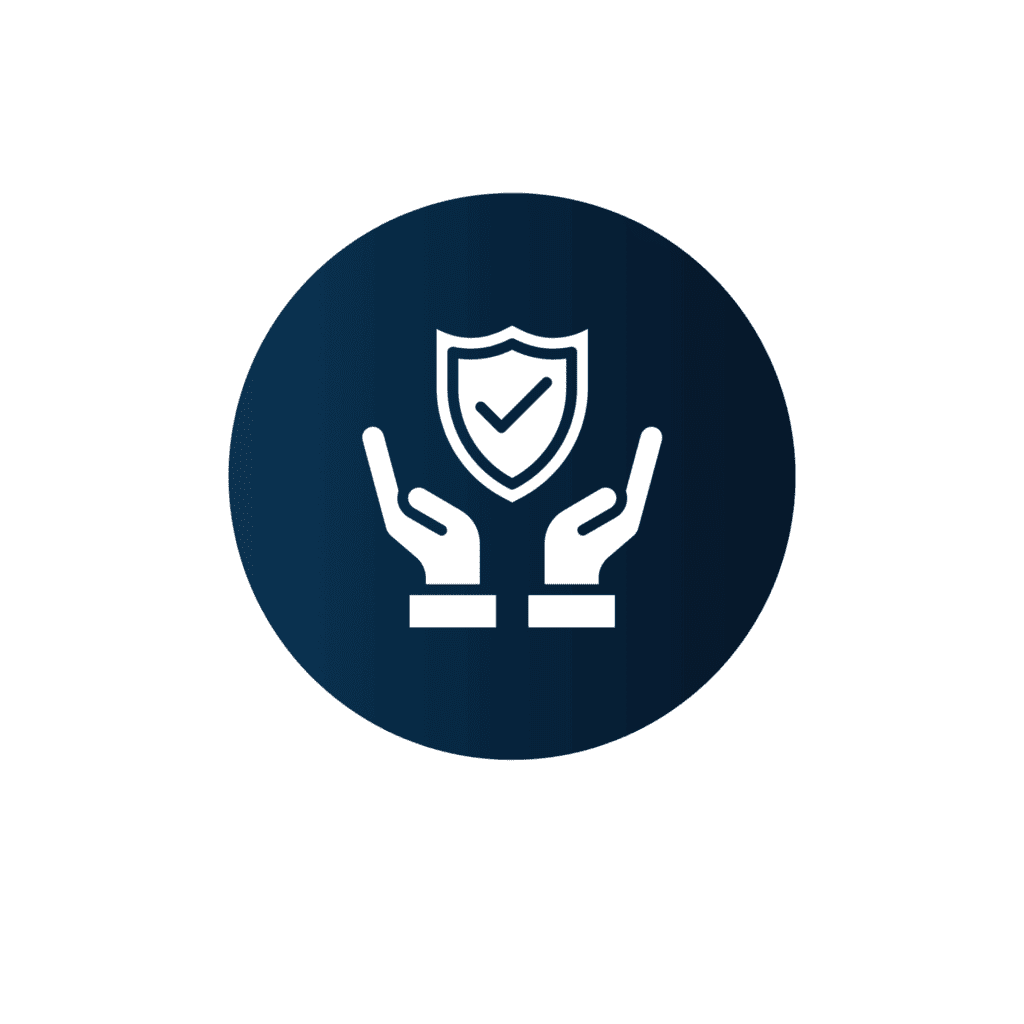
Safety
Floor flatness assessment in high density storage and sports’ facilities to identify area of surface settlements that may cause safety hazards.
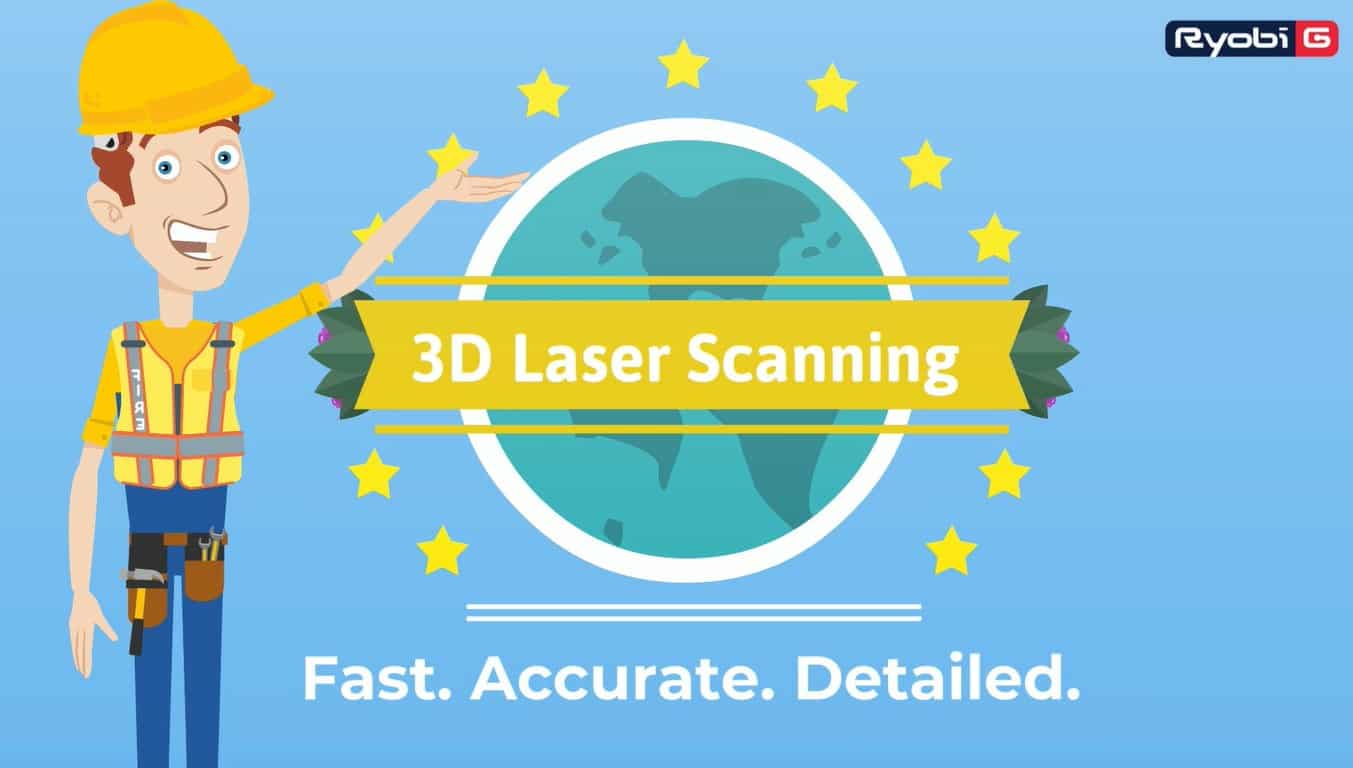
Confidence in every decision.
With a team of professional and cutting-edge 3D laser scanning equipment. Ryobi-G provides 3D laser scanning services that help you document your room, building, or structure safely, efficiently economically.
Instead of working with outdated building plans or field measurements, with 3D laser scanning technology all of your designs are based on true-to-life measurements and conditions.We makes analysing and navigating structures simple for you especially whenever you need precise measurements that can be visualised.
Benefits of our 3D laser scanning
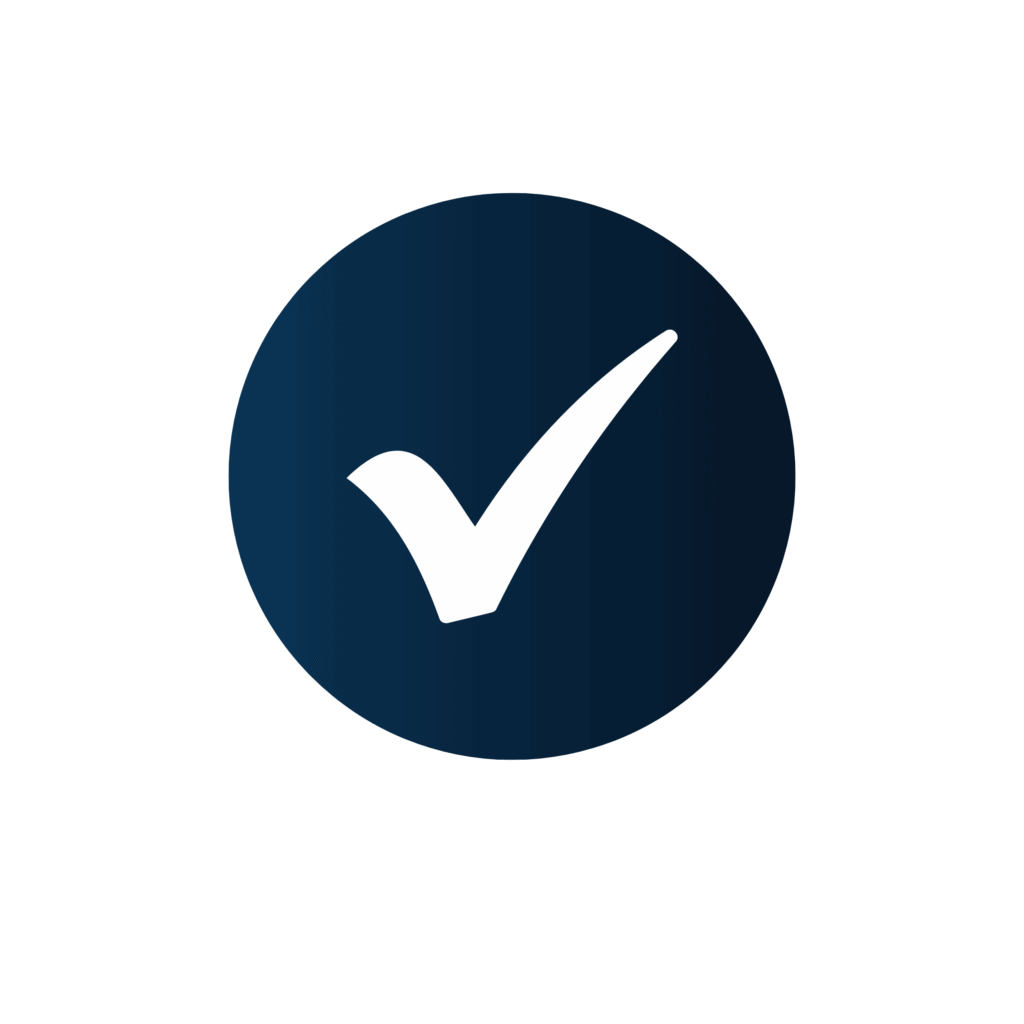
Accurate
Precise measurements with an accuracy of up to ± 2 mm*.
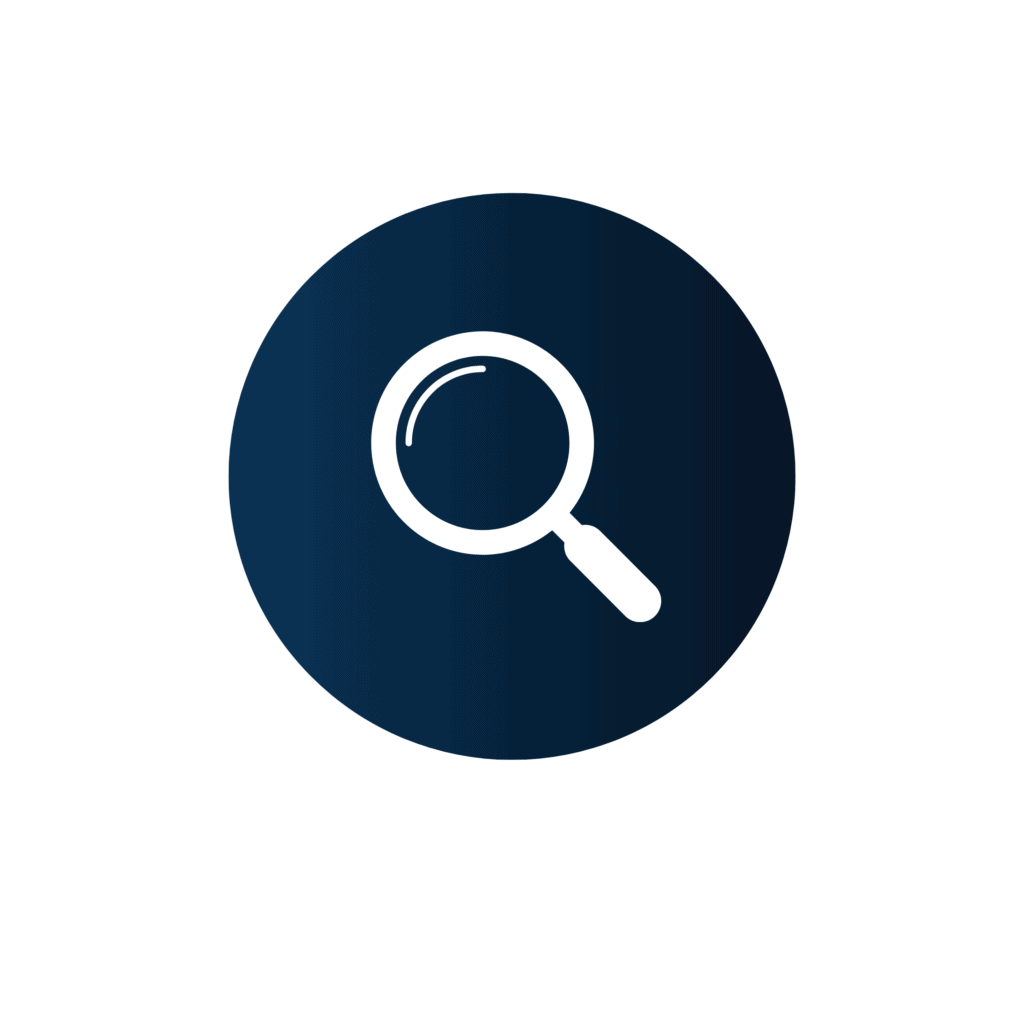
Detailed
Our attention to detail and precise 3D laser scanners assures that our scans or not only accurate, but rich in detail
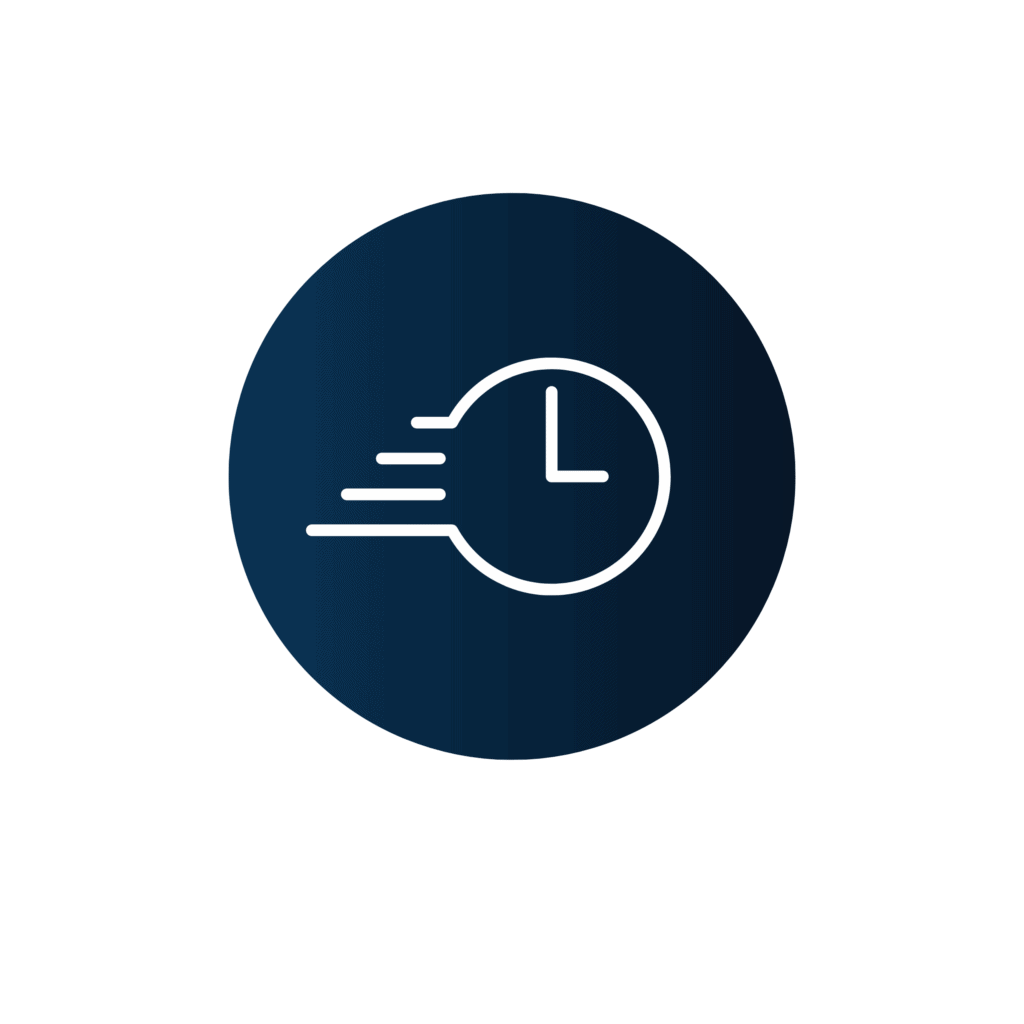
Fast
Being able to capture thousands of points in seconds, we are able to cover a large amount of surface area in a relatively short amount of time.
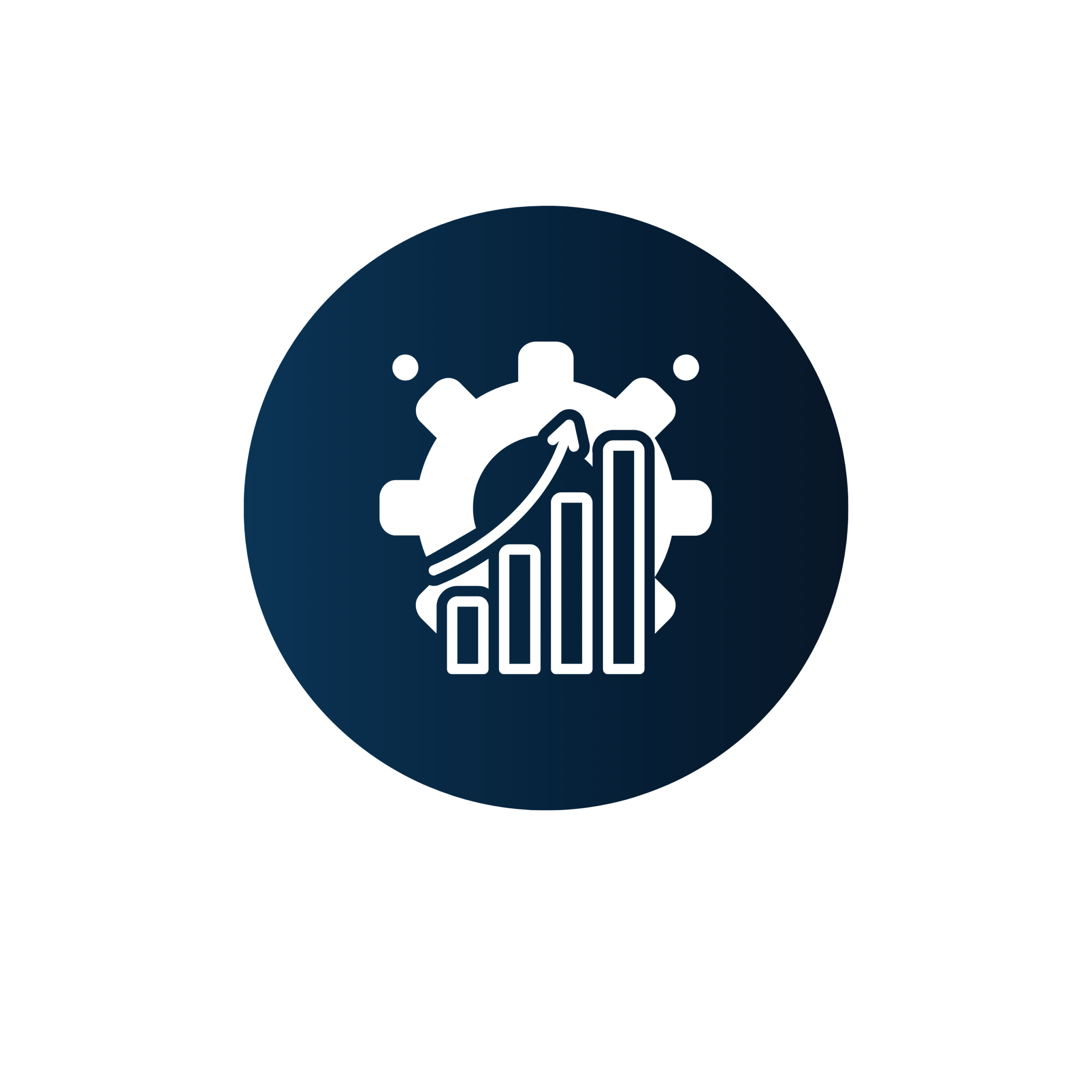
Efficient
Onsite data-capture time is reduced significantly and the accuracy of 3D laser scanning eliminates the need to revisit the site for missing measurements.
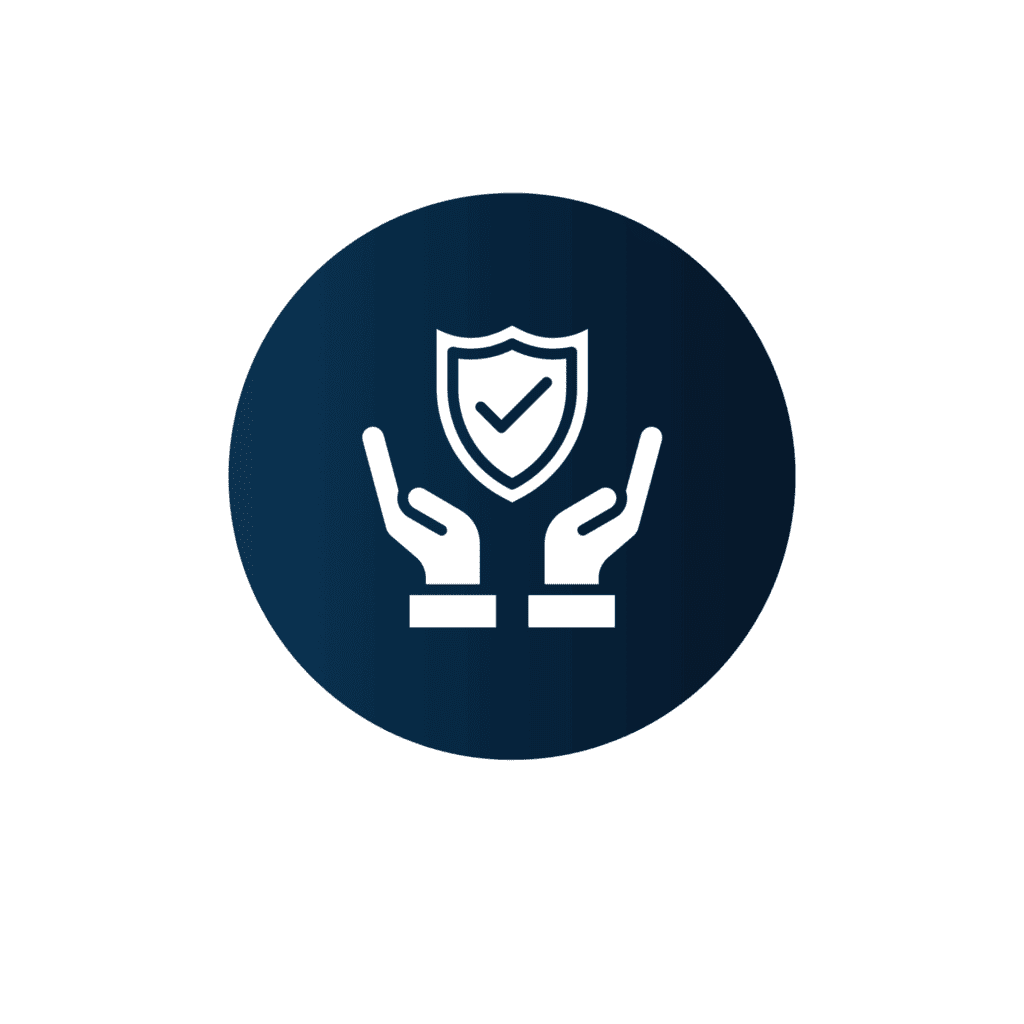
Safe
Fast data capture and remote sensing ability of 3D laser scanner helps to minimize crew’s exposure to harmful environment
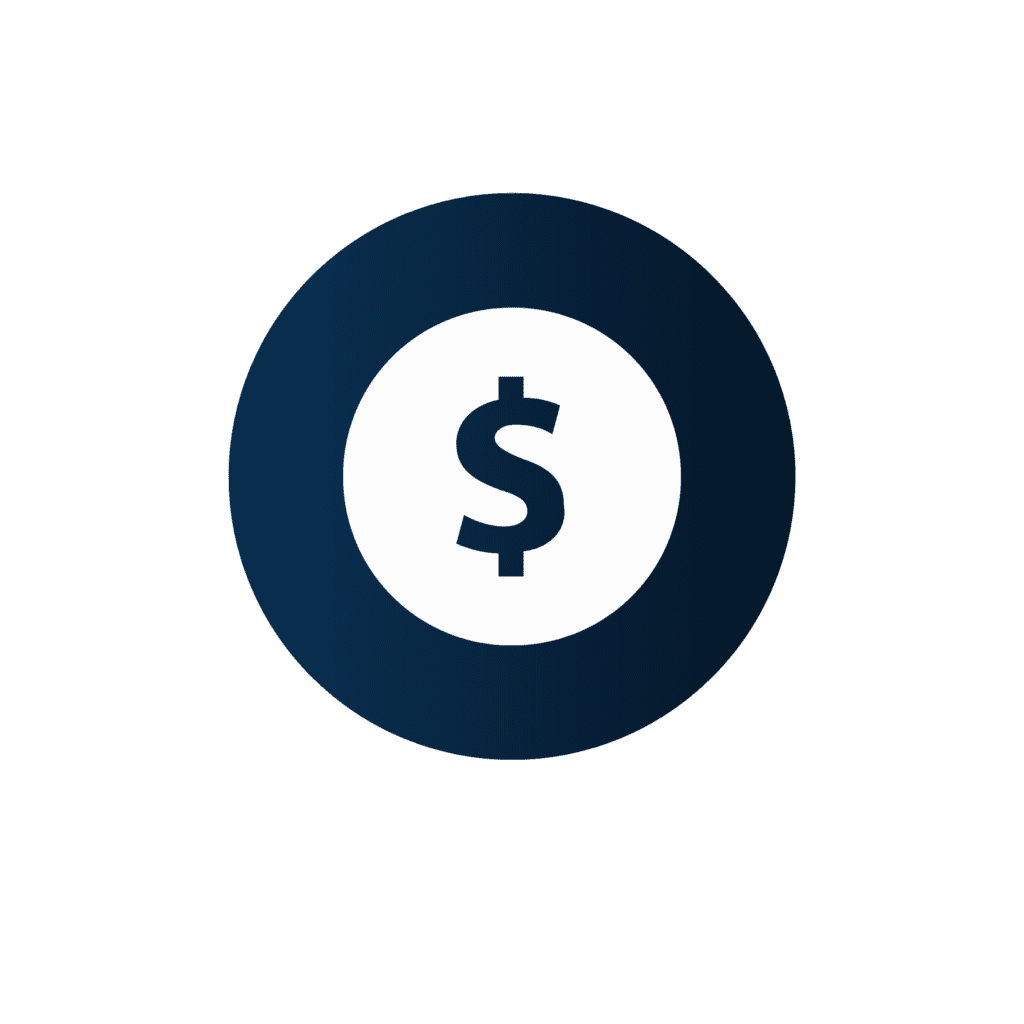
Economical
With less time and labor is spent on-site, minimal disruption and downtime of facilities, 3D laser scanning is substantially more cost-effective than most other measuring technologies.